ROBOTIC APPLICATION OF ADHESIVE

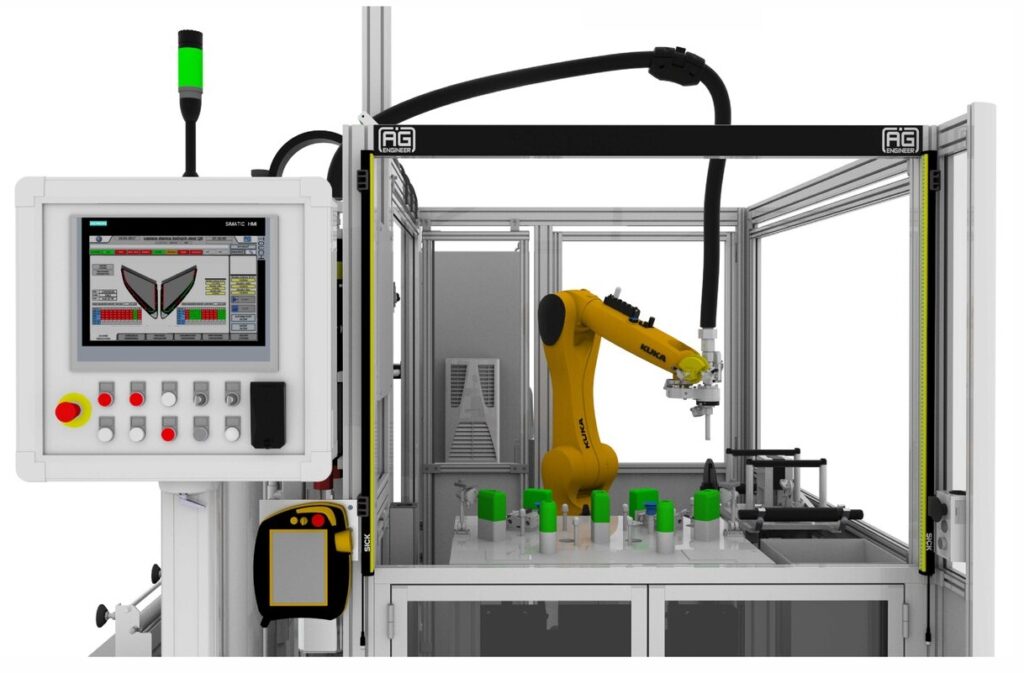
The side window adhesive station is used to apply adhesive to the 2 x Audi Q8 side windows. The station applies adhesive with robotic system on both side windows in a row in one process with application head. We used a special rotating application head with nozzle which applies adhesive to a precisely defined place on the glass, determined by a primer.
The interesting thing about this workplace is that the worker directly loads the side glasses through the zone of SICK safety barriers on the centering table, which is located in the working zone of the robot. The glasses are placed on table. There is a locking and centering system with pneumatic elements on the top. Each glass is secured with a suction cup, which is under the glass and both can be controlled independently by foot switches.
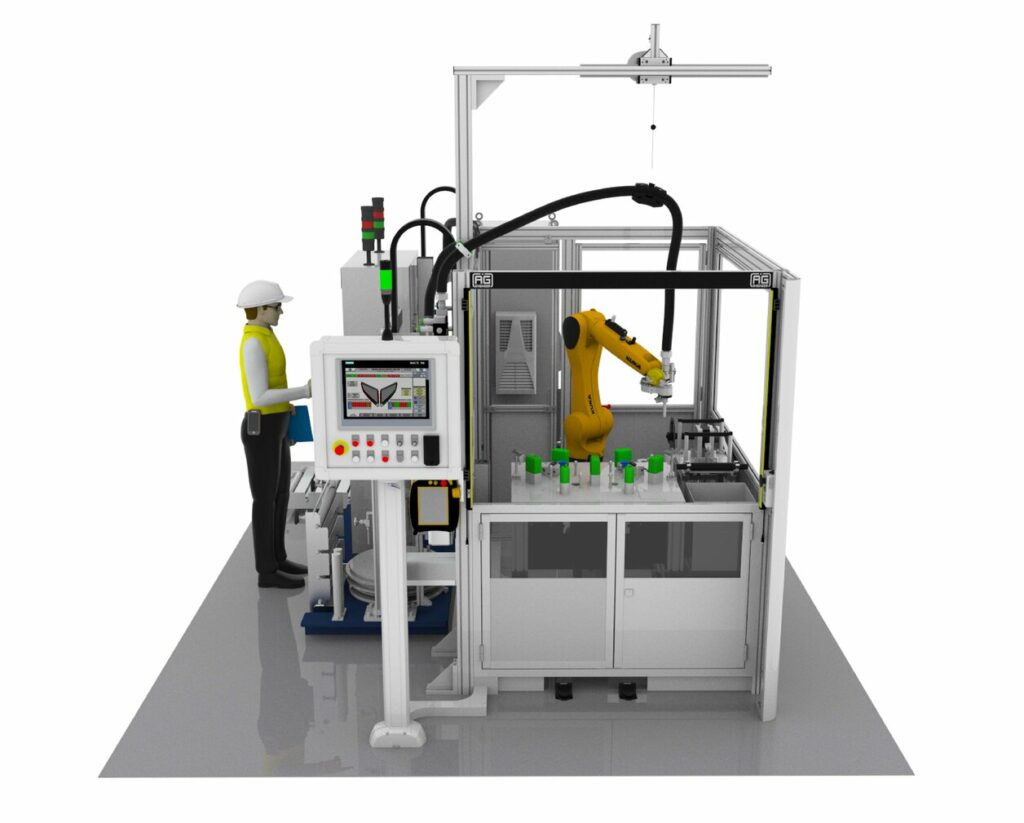
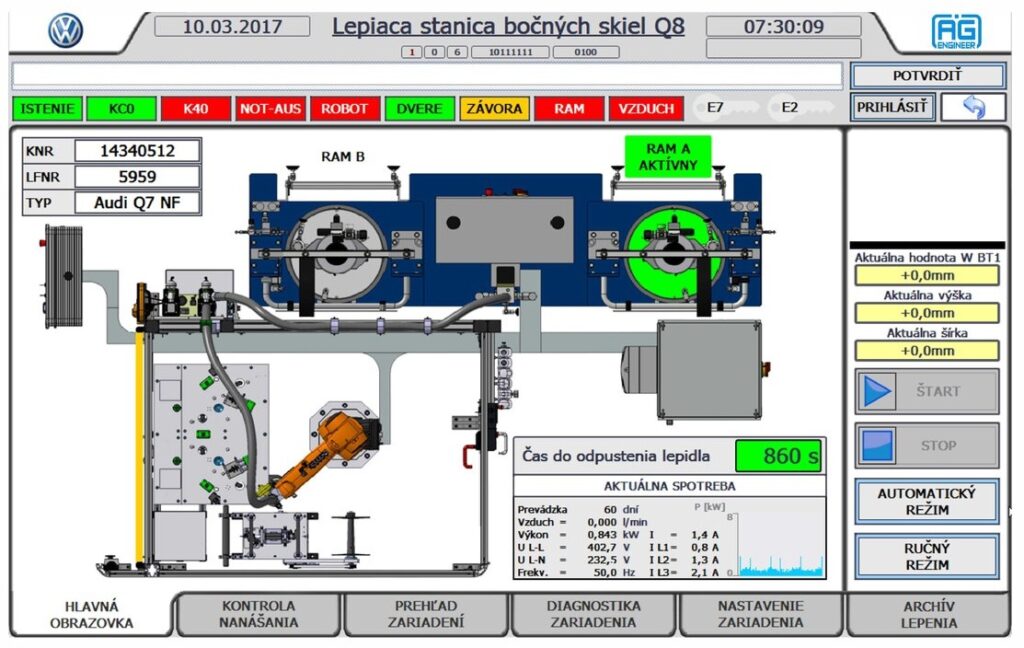
When the window is placed on the suction cup between the centering stops and the worker leaves the safety zone with his hands, its position is automatically secured. After this operation, the pneumatic cylinder is tightened, which centers the glass in the starting position. The correct position of the glasses is evaluated by a laser distance sensor, which detects the edge of the window. At this point, the system receives a signal that the glass is ready for glue application. If the glass is not evaluated as “Ready for the application of glue“, it is necessary to release the glass with the foot switch and repeat the procedure. After leaving the safety barrier area, it is necessary to confirm with the button so that the process of applying the adhesive by the robot can begin.
The robot automatically applies the glue in the programmed trajectory. The end of the process of the application is signaled by a lit LED lights in green. The LED stripes is located on the construction of the workplace fencing. The worker takes the window with the applied glue from the centering table and places it in the body of the car which is located on the conveyor system. There is a cleaning station in the workplace, in which the robot automatically cleans the application nozzle after each process. This station contains an unwinding system for a roll of paper, which needs to be refilled by the operator.
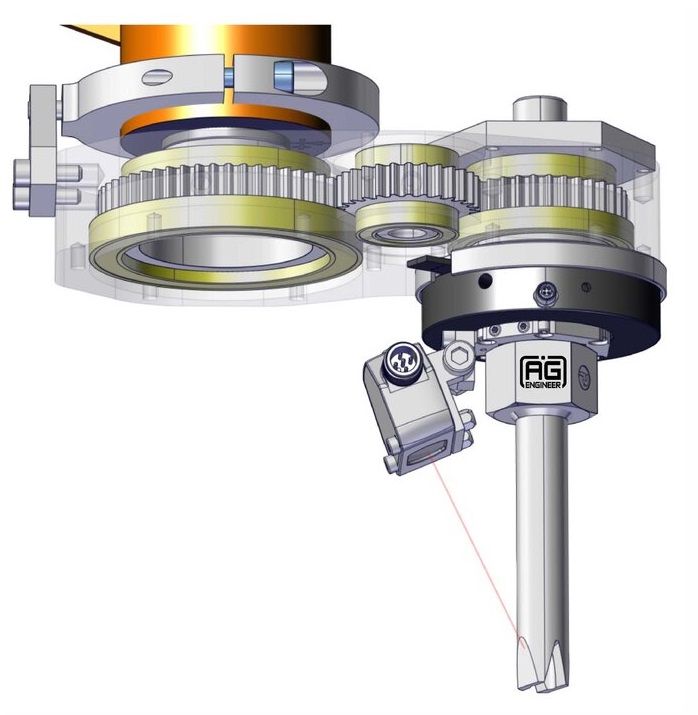
The application head is located on the flange of the last axis of the Kuka robot. It is designed so that it is possible to rotate the application nozzle +/- 360 ° and at the same time the adhesive passes through the closed system. This movement is ensured by a system of gears which is located in the housing of the application head. With this system we can ensure application of the adhesive in the required profile (triangle cross-section) along the entire application trajectory. The height of this adhesive profile is evaluated by a laser sensor, which measures its height just behind the outlet of the application nozzle, where the trajectory of the application of the adhesive begins to form. This system and the movement of the application nozzle are shown in the following video.
In the back of the workplace there is a system of “RAM” stations, which ensure the supply of glue to the application head of the robot. The system is designed with two containers, where barrels filled with special glue are replaced. Each station has a pressure system that drives the adhesive through the pipes directly from the barrels through the pumps to the application head. The application head has a special connection for a flexible hose, which is lightened by being lifted by a balancer located on the arm above the workplace.
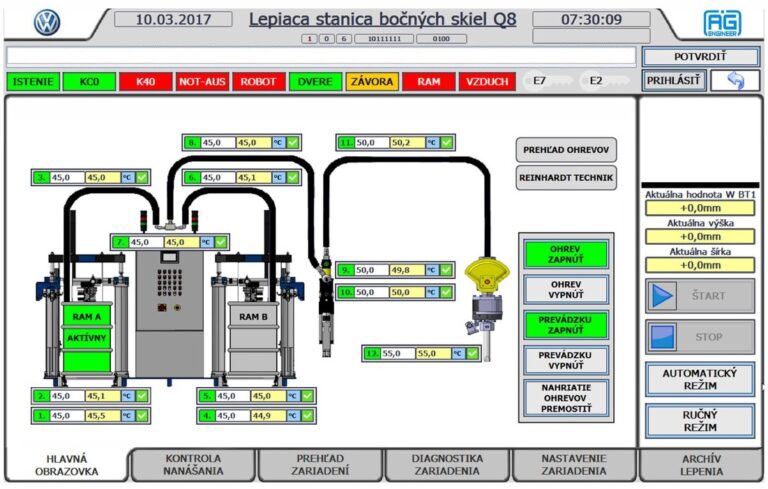
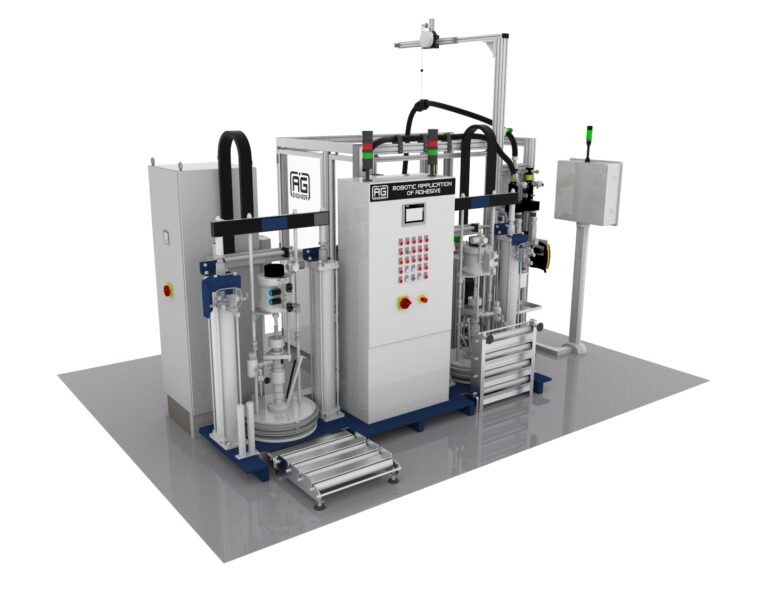
In front of the workplace there is a rotating stand on which the Siemens TP 1500 touch control panel is placed. The visualization of this application is created in the Tia Portal V13 program which is running on this panel. It displays all the necessary data, device status and also serves to control the entire automated workplace.
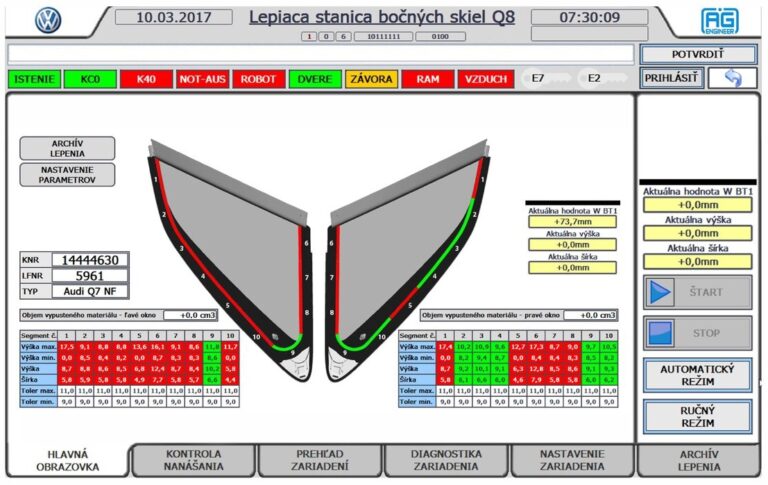
About us
Our company operates in the field of industrial automation. It deals with design, development, design, wiring and filtered engineering, according to customer requirements.
When solving projects, we work with the latest technologies, we provide comprehensive services from design to delivery of equipment to customers. Of course, our work is the delivery of the necessary documentation and training for the operation and maintenance of the supplied equipment.
The company further specializes in the implementation of specific applications, such as integration work and optimization of device functionality. AG Engineer is a guarantee of a complete systematic solution for your production.