
Some of our realized projects !
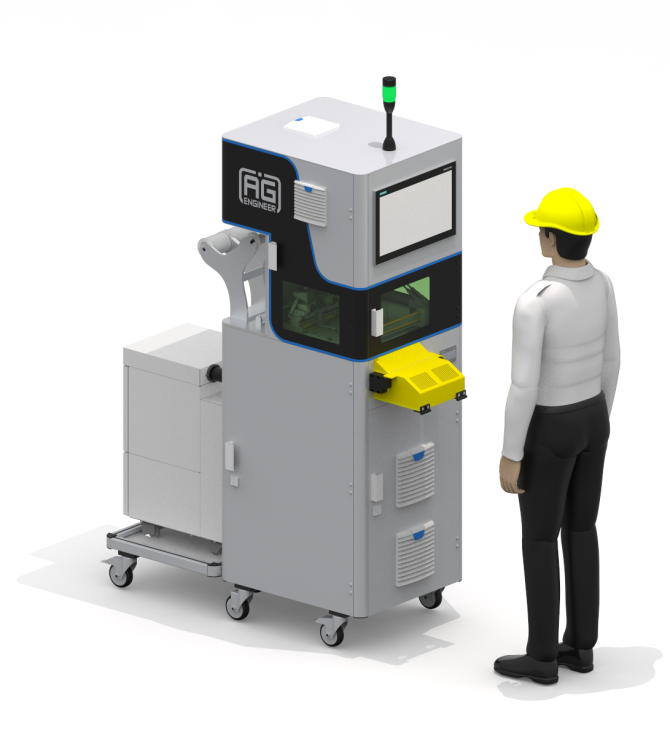
LASER STATION OF PRODUCTION LABELS V2.0
The V2.0 laser marking station is used to laser TPS labels on the marking tapes, which are then glued to a designated place on the vehicle body. The station has two tape tracks and a lockable tray for TPS labels. The marking is performed using an OEM TruMark 5020 laser unit from TRUMPF.
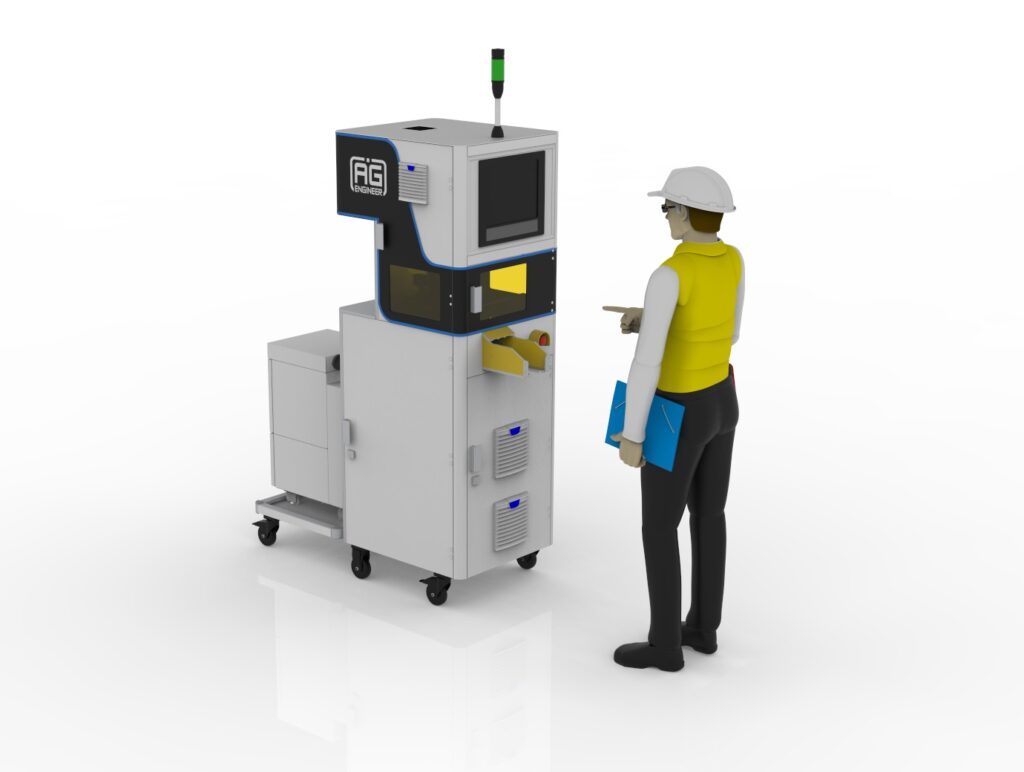
LASER STATION OF PRODUCTION LABELS V1.0
The laser marking station is used to print a TPS label on the marking tape, which is then glued to a designated place on the vehicle body. The station has one tape path and one tray for TPS labels.
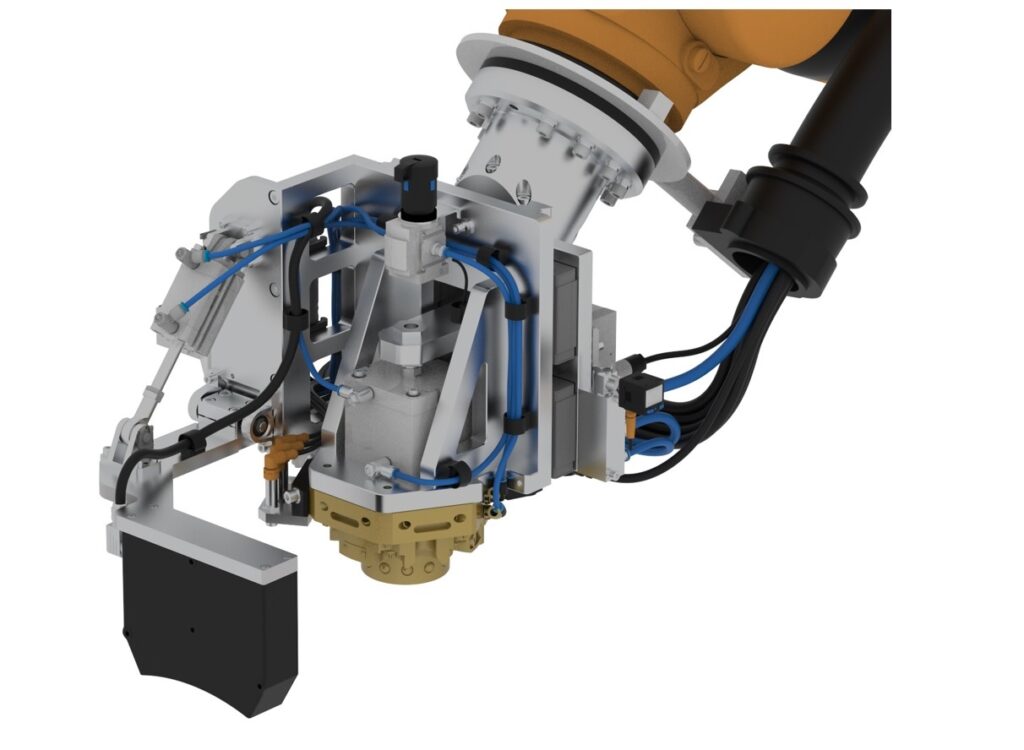
ROBOTIC CAMERA SYSTEM FOR VIN NUMBER RECOGNITION
After opening the hood with a device designed for this purpose, the robot with a camera on the tilting arm moves under the front hood, where it performs the measurement. If the camera system evaluates that the area for marking the VIN number is OK, the robot continues to operate – it moves under the hood with the marking head and do the process of marking VIN number.
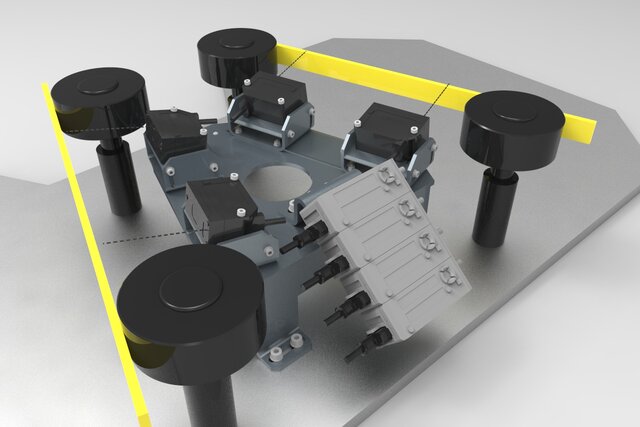
SIDE WINDOWS TYPE RECOGNITION
The device consists of several mechanical, electrical and optical parts, which are interconnected and controlled by a PLC system. The main part of the device are four optical laser sensors designed to measure distance. The sensors, together with their control units, are placed on a large mounting plate, on the table of the centering device.
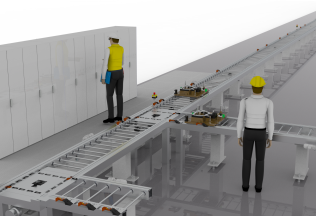
CONVEYOR SYSTEM
Device is design to control the movement of semi-finished car gearboxes along the conveyor system of the production line. The device works on the basis of unambiguous identification of the position and condition of the pallet with the gearbox during the entire process of its production.
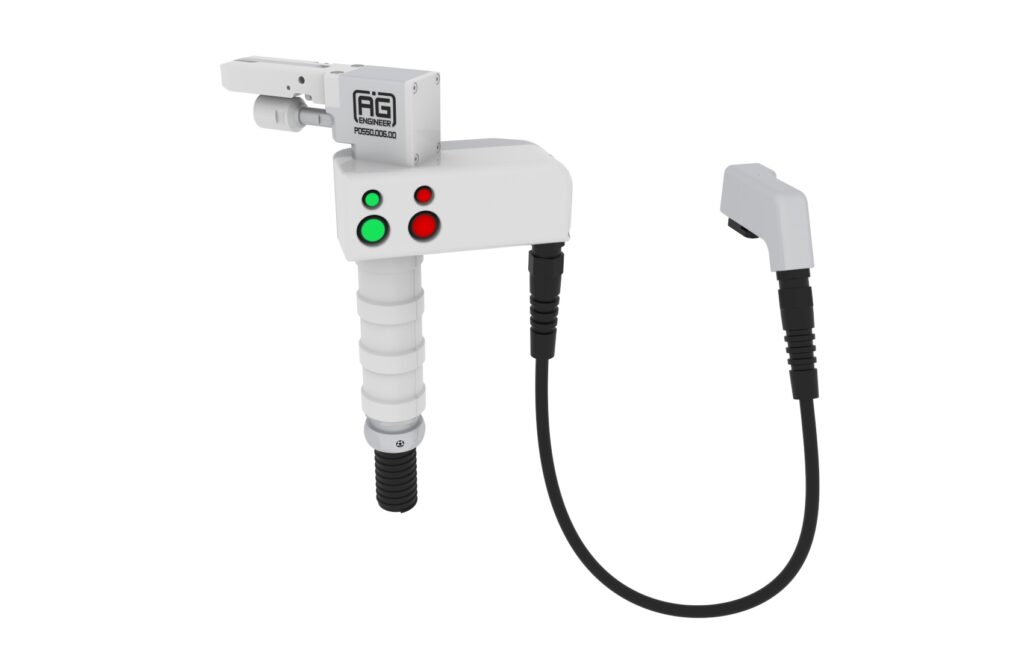
FILLING ADAPTERS
Adapters for filling media such as oil, petrol, diesel, air and other liquids in various forms. They are developed based on specific customer requirements. The main criteria for the production of adapters are: reliability, safety and ergonomics for comfortable work.
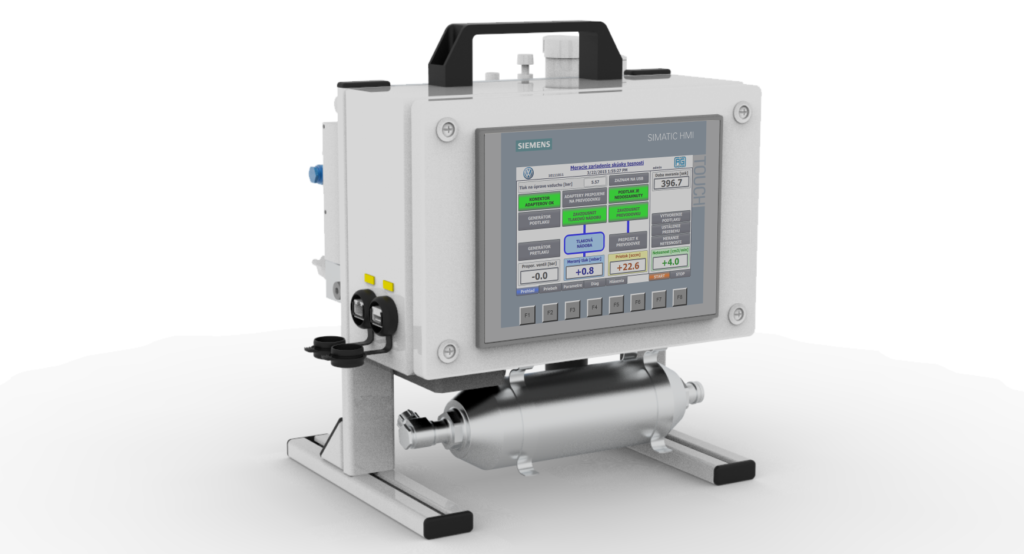
LEAK TEST 1.0
The device is portable and requires 230V from the standard electrical network and 6 bar compressed air for its operation. It uses two measuring principles to measure tightness, based on measuring the pressure difference during the measurement period and the air flow between the measuring device and the gearbox.
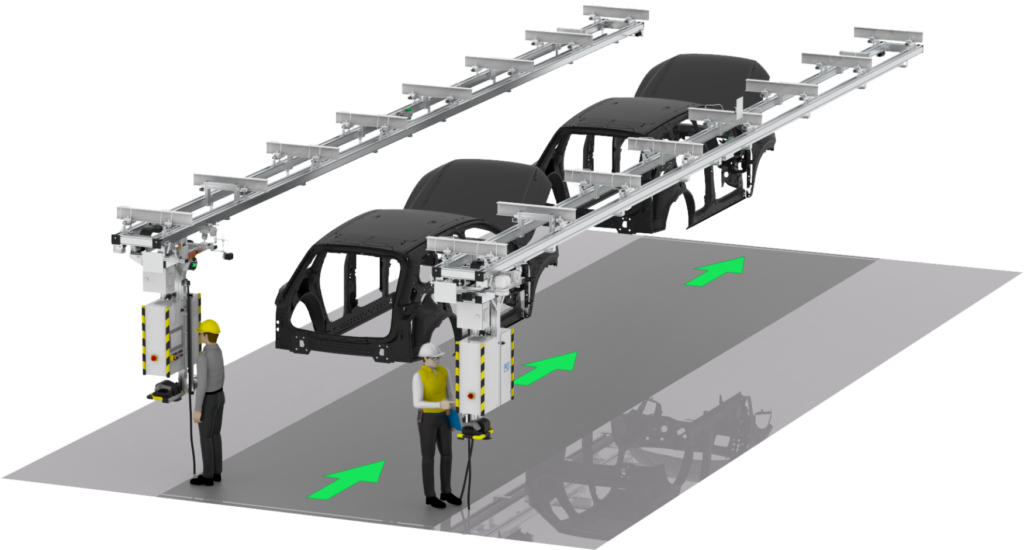
AUTOMATED AIR FILLING FOR SHOCK ABSORBERS
The LFA1012S filling device is used to fill the vehicle’s air suspension system. Each console is equipped with a traction motor and safety features. The device is located on the ML04 line in the Volkswagen Slovakia, Bratislava plant and it is possible to fill the air suspension of the VW Touareg, AUDI Q7 and AUDI Q8 with it.
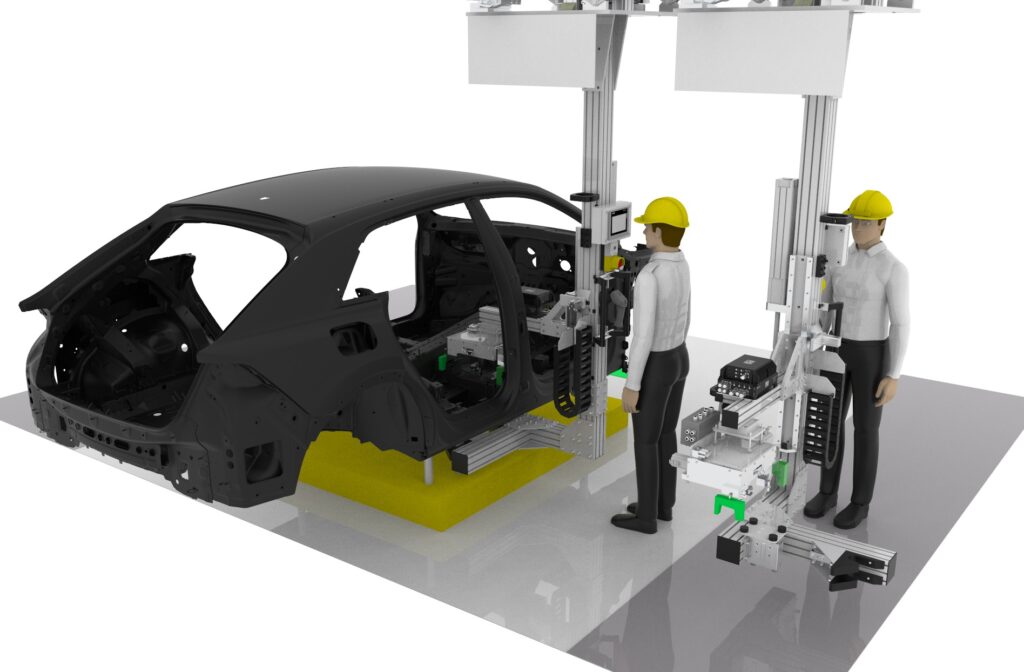
EMERGENCY STRATEGY MANIPULATORS FOR VIN NUMBERS MARKING
The workplace is located in the production hall of VW Bratislava. It is used to VIN numbers marking into the body of Q8, Q7 and VW Touareg. The workplace consists of two separate manipulators. The first manipulator in the direction of travel of the line is used to stamp the VIN number into the body of AUDI Q8, the second manipulator is used to VIN number marking into the body of AUDI Q7 and VW Touareg. The devices serve as an emergency strategy, ie in the event of a failure on the automatic stamping device. The automatic VIN marking workplace is located in front of the KB line and the KUKA robot guides the tool with the punching head into the body.
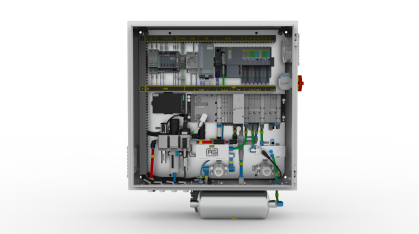
LEAK TEST 1.5
The tightness test device is a serial device designed for continuous operation, powered by 230V from a standard electrical network and 6 bar compressed air. To convert the leakage value in units [cm3 / min], the leakage conversion characteristic is used, for each method separately.
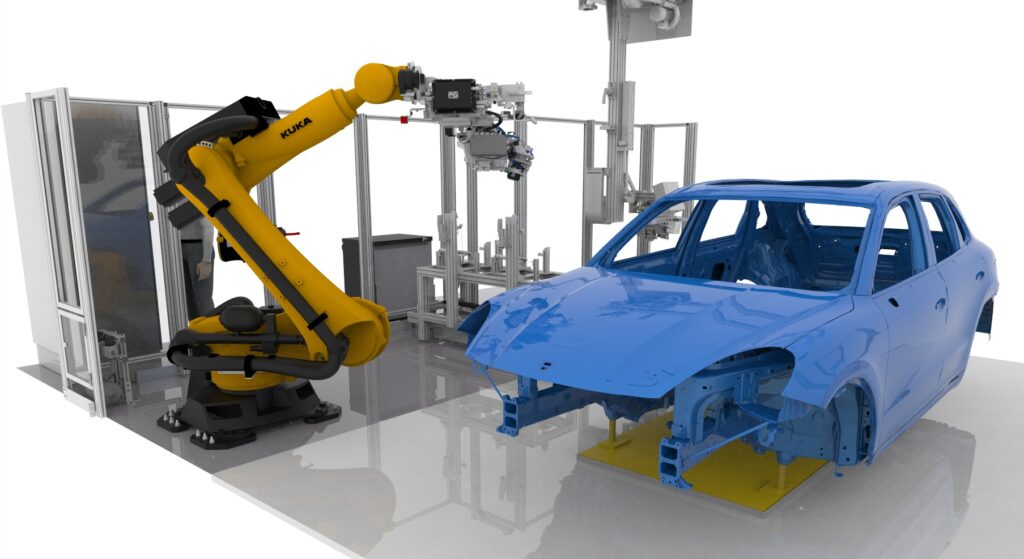
ROBOTIC VIN MARKING WORKPLACE
Fully automated workplace of the process of VIN numbers markingon the body. The robot positions the marking head using a camera system and punches the VIN number to the specified location. The workplace is enclosed by fencing and contains sophisticated security elements for the protection of workers and the process of VIN numbers marking.
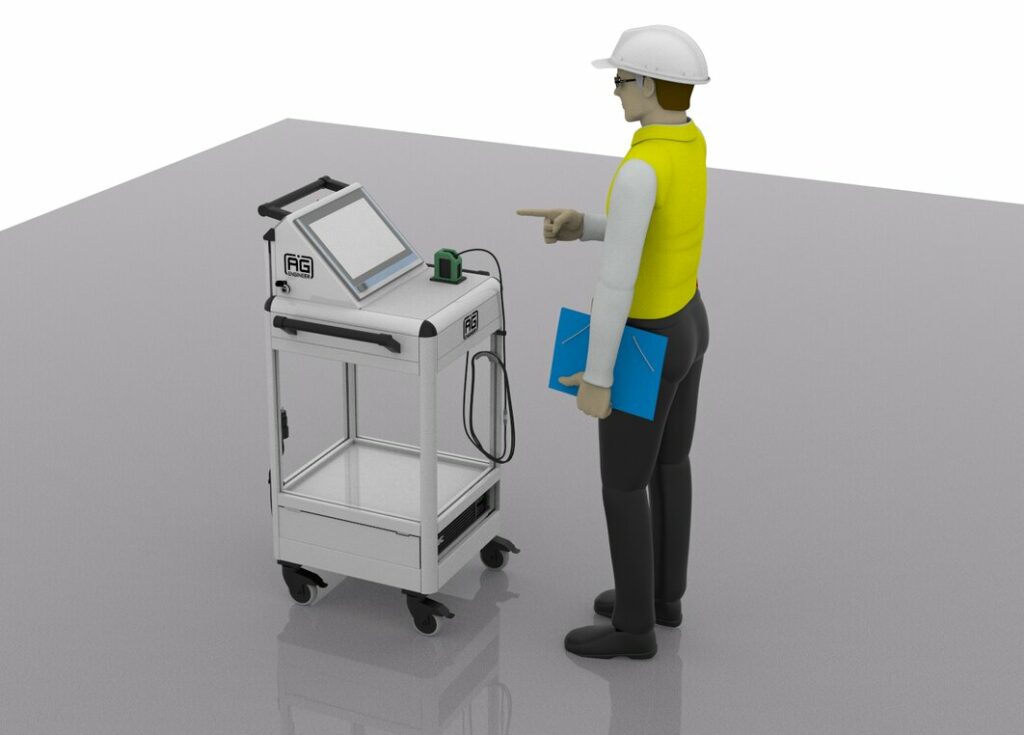
COMPACT VIN NUMBERS TEST
The device is used to check the stamped VIN number. After stamping the VIN number into the body with an embossing device, it is necessary to check it. The KEYENCE LT-9011M manual distance sensor with a range of + 0.3 / -0.3 mm is used to check the depth of the groove.
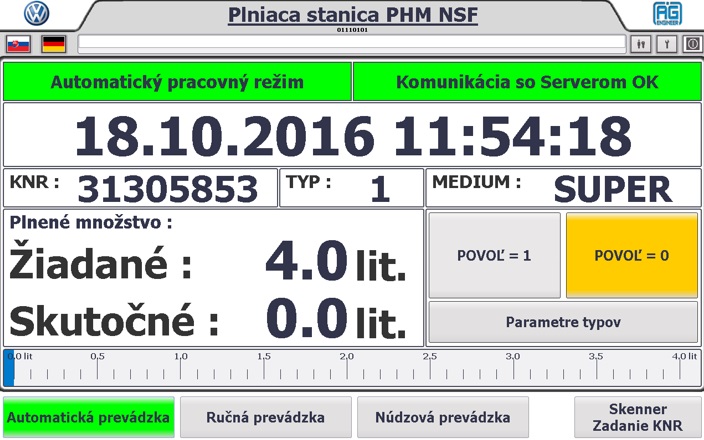
REFUELING STATION CONTROL
The NSF filling station is used for refueling NSF vehicles with SUPER and DIESEL fuels on the ML03 assembly line. It consists of a refueling stand and a switchboard on which the control panel of the SIMATIC Comfort Panel is located.
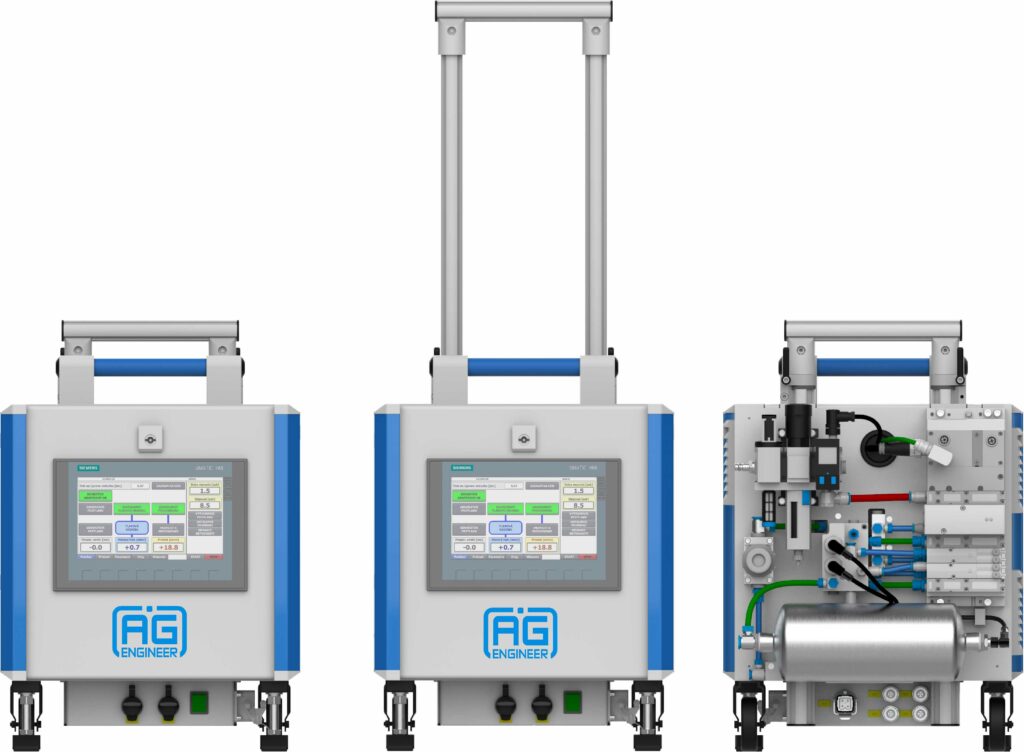
LEAK TEST 2.0
LEAK TEST 2.0 is a device designed for accurate evaluation of tightness and volume for a wide range of products and applications. It can measure the leakage of air or other media in closed products that have been welded, glued, pressed or folded into a closed unit in the previous process. The measured volume with the help of the LEAK TEST 2.0 device is very accurate and quickly evaluated on the basis of comparing the conversion of measured values.
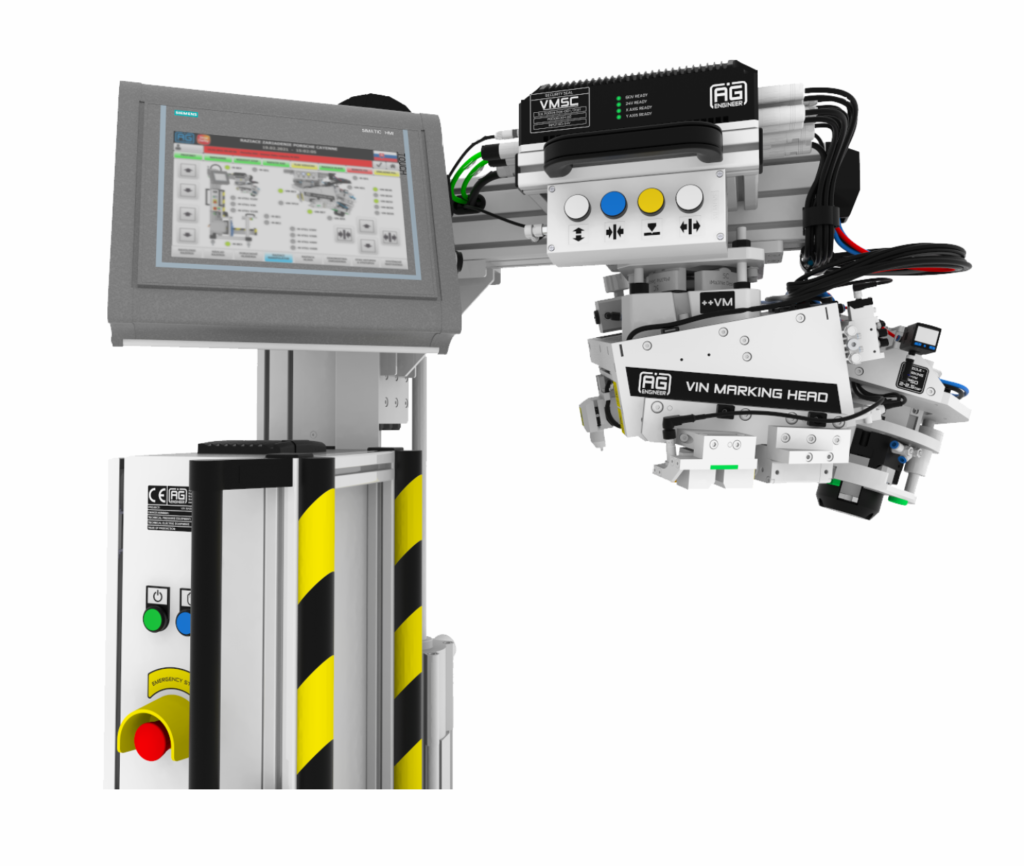
PORTABLE VIN NUMBER MARKING SYSTEM
The mobile VIN number marking system is intended for marking VIN numbers for Porsche Cayenne. The device is operated by one worker who guides the punching head by means of stops into the open body. The embossing head is on the upper movable arm and with the help of the lower arm and clamping systems it is attached to the body on which the process of embossing the VIN number is performed.
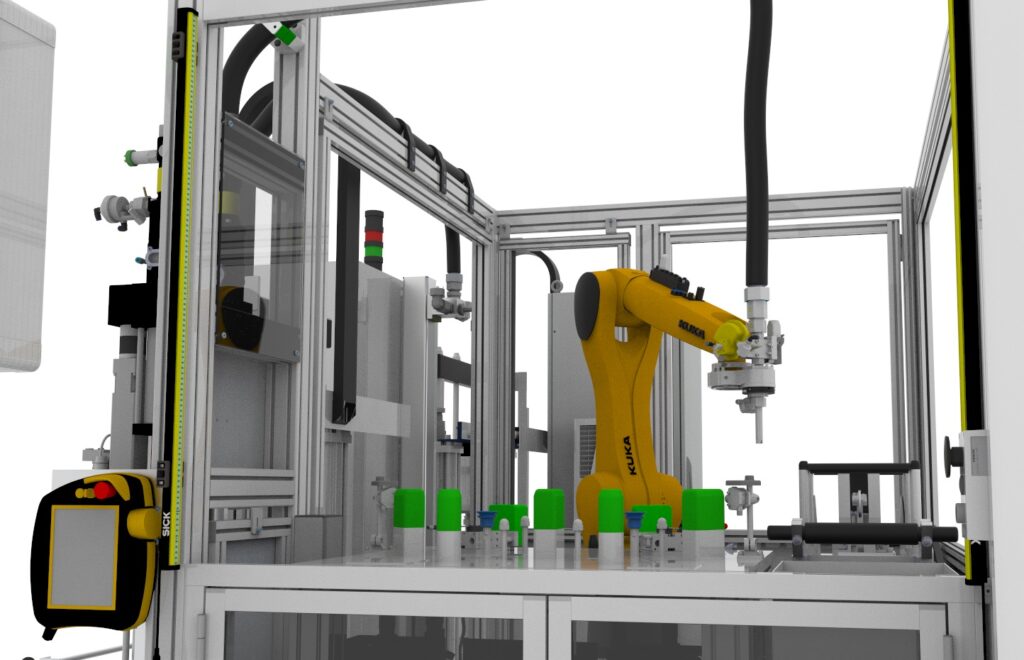
ROBOTIC APPLICATION OF ADHESIVE
The side window adhesive station is used to apply adhesive to the 2 x Audi Q8 side windows. The station applies adhesive with robotic system on both side windows in a row in one process with application head. We used a special rotating application head with nozzle which applies adhesive to a precisely defined place on the glass, determined by a primer
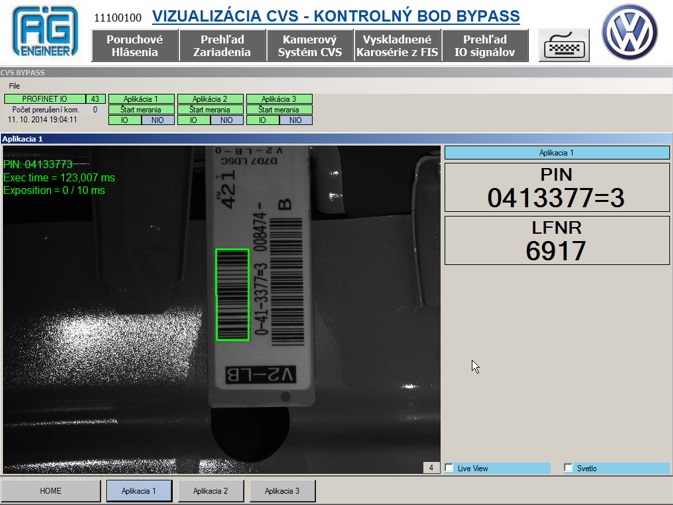
BODY TYPE RECOGNITION BY CAMERA SYSTEM
The application is used to distinguish 22 types of bodies from bodies of other types in the main tank and then move to another transport branch. When the body arrives at the checkpoint, a snapshot of the TPS label is taken. By analyzing the image, you get the PIN number of a specific body. Based on the PIN number obtained, the request is sent to the FIS database to the “Laufende Nummer” and the type of the corresponding bodywork.
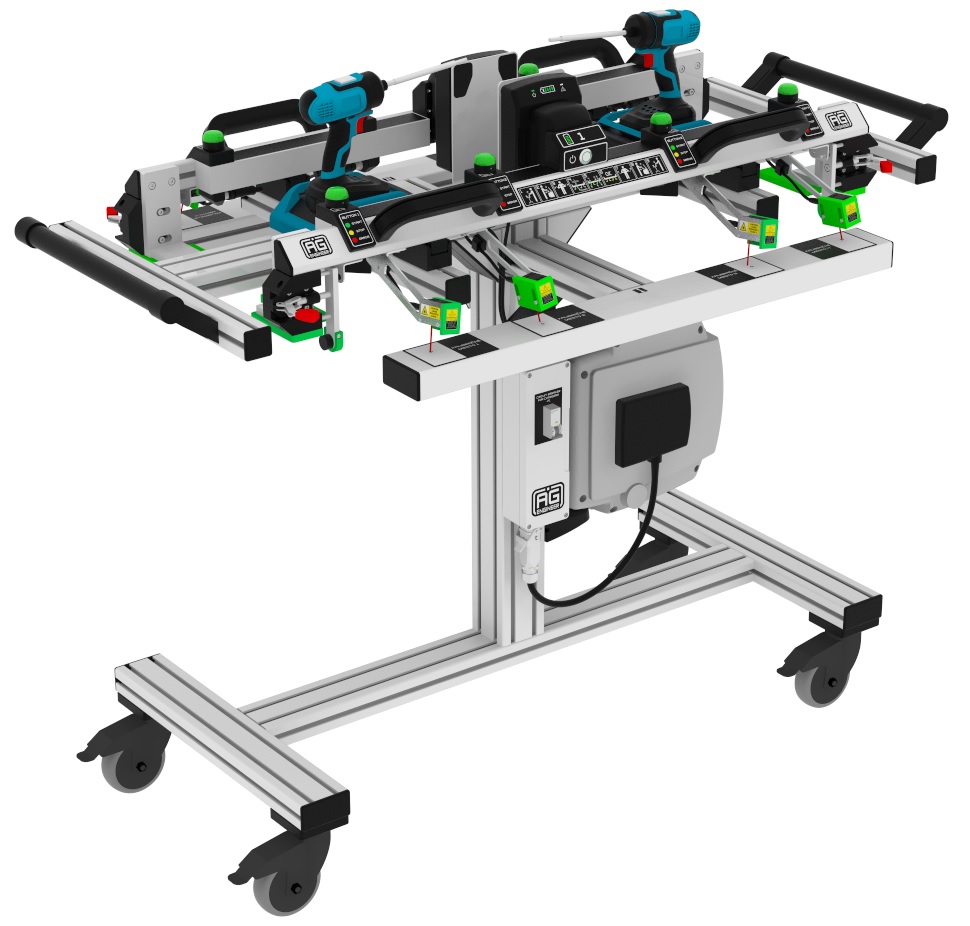
ADJUSTING THE POSITION OF THE SEALING PART
The measuring device is used for precise adjustment of the four adjusting elements. It consists of two wireless measuring jigs, two wireless logic screwdrivers and a charging (docking) station. The unit evaluates the values from the sensors and controls the screwdrivers so that the screwdrivers are flushed to the worker when he reaches the required height.